6 Torsion
Introduction
Click to expand
Torsion is a moment applied around the longitudinal axis of a body. The effect of torsion is a twisting action. Torsion is found in many common situations. Some examples of applications in which torsion is a primary form of loading include:
- In machinery, rotating shafts, such as transmission shafts that transmit power, are subjected to torque
- When one uses a torque wrench to tight or loosen a bolt, the bolt is subjected to torque
- Poles on which road signs and traffic lights are mounted are subjected to torque when forces (such as wind) are applied perpendicular to the sign (Figure 6.1).
- Hinge pins are subjected to torque when the rotating elements they are attached to (doors for example) are rotated.
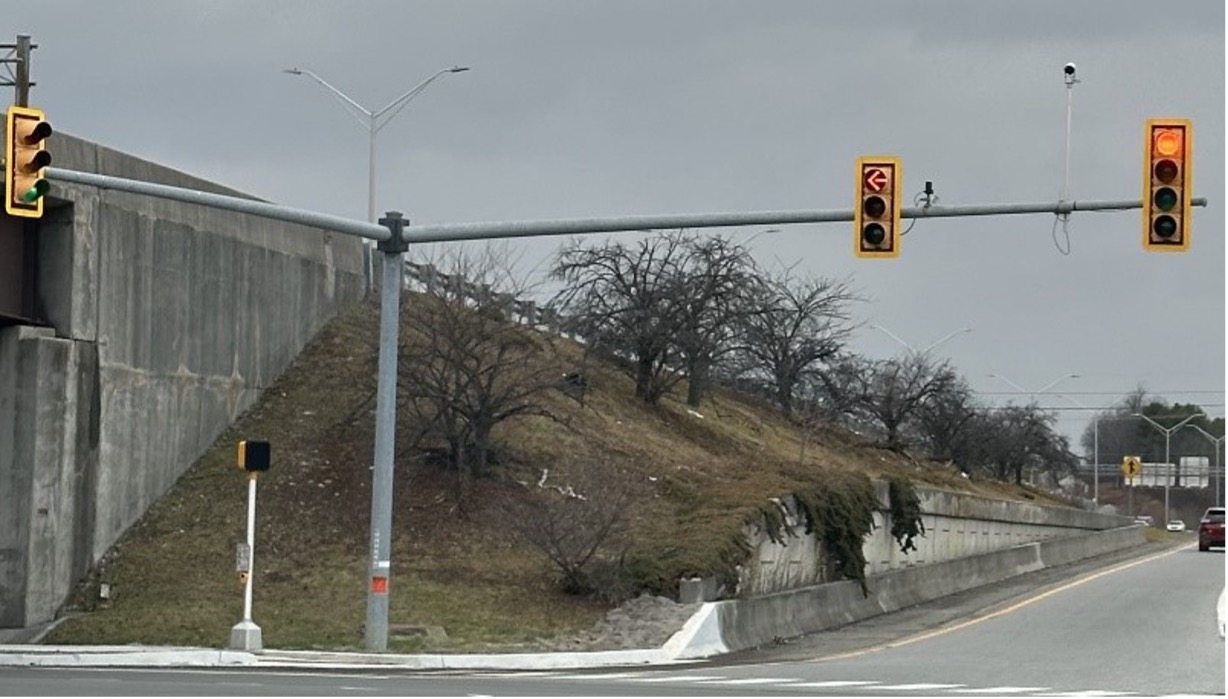
This chapter will focus on bodies subjected to pure torsion (no axial or bending loads). These concepts will appear again in Chapter 14 when more generalized loading conditions are discussed.
In Section 6.1 and Section 6.2 we’ll derive equations for calculating the stress and deformation caused by torsional loads. In Section 6.3 we’ll consider statically indeterminate torsion problems, using methods similar to those in Section 5.5. In Section 6.4 we’ll consider torques due to power transmission, a common application where torques are present.
6.0.1 The Effect of Torsion
As mentioned above, the effect of a torsional moment is to cause the body to twist. The resulting stress is a shear stress.
Consider the pleated tube shown in Figure 6.2 below. @fig6.2 (A) shows the tube in an unloaded state with some of the pleats colored for identification. In Figure 6.2 (B), we see that after a torque is applied, the pleats move vertically but not horizontally. In addition, without the color present, it would be difficult to identify the displacement at all. We can say that all points remain in their original plane even in the deformed state so that the shape of the cross-section is unchanged.
.png)
Now consider the I-beam subjected to torsion in Figure 6.3. In this case we see that the shape of the cross-section changes and that the points do not remain in the same vertical plane (there is horizontal displacement as well as vertical). This shape change is referred to as warping. In this text, we will only be considering circular cross-sections with no warping.
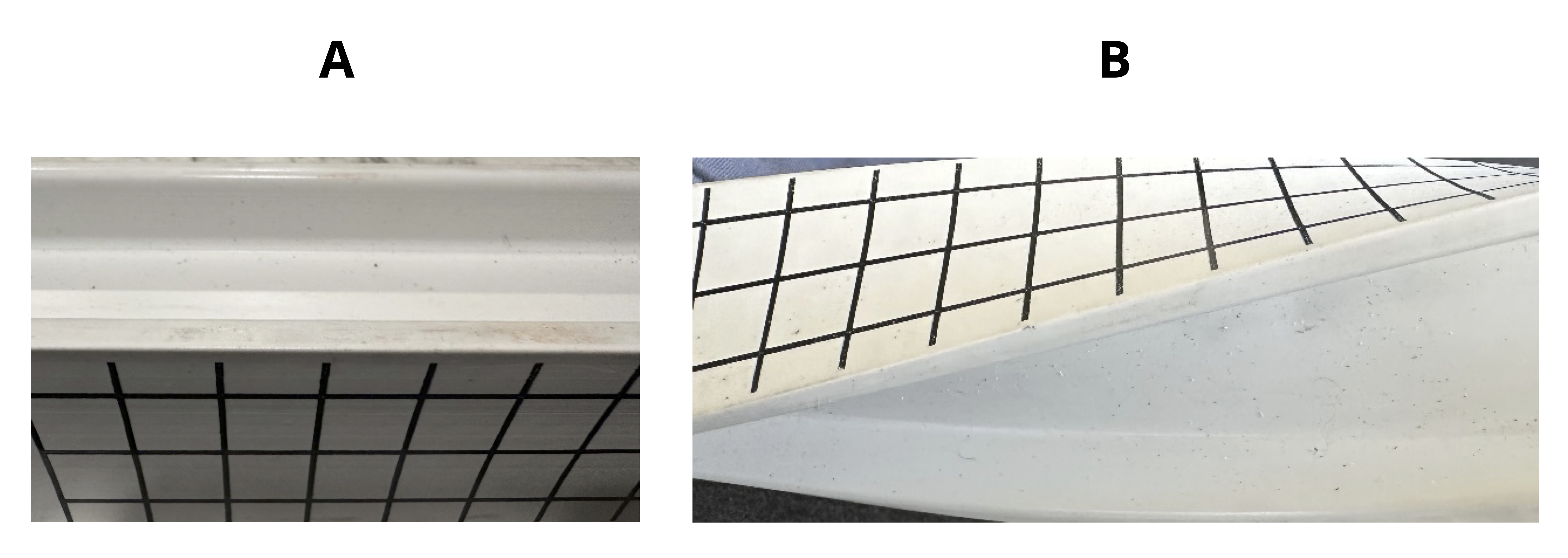
Going back to Figure 6.2, let’s consider the shape formed by the non-displaced colored lines in Figure 6.2 (A) versus the displaced lines in Figure 6.2 (B). These images are shown again in Figure 6.4. In the non-displaced case, a rectangle can be drawn around the green lines on the left with 90° corners. In the displaced case, the corners are no longer at 90°. From Section 3.2, we know that this change in angle is the definition of shear strain. The evidence of shear strain indicates that the applied torque results in shear stress.
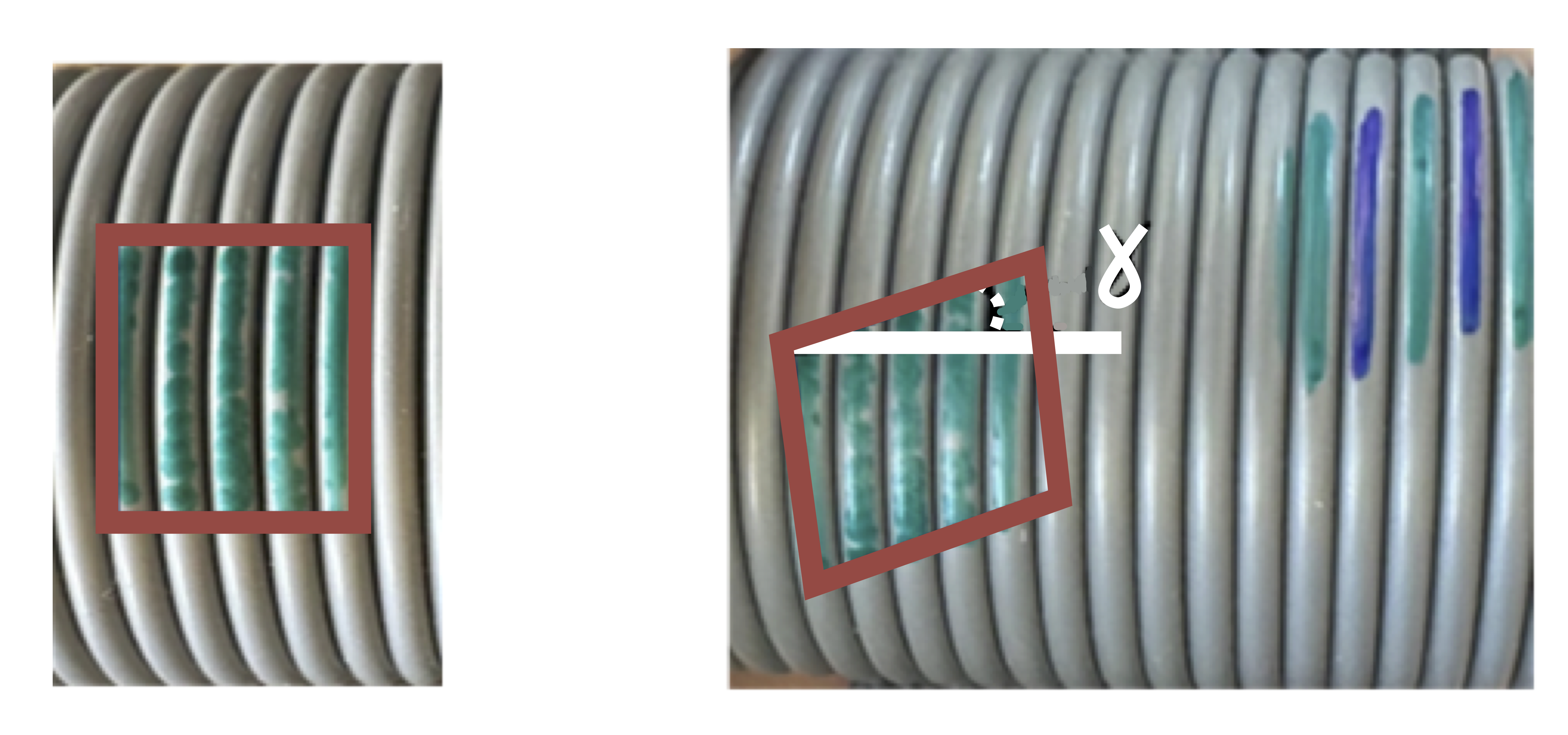
6.0.2 Determination of Internal Torques
As with axial loading, the stress and deformations due to torsion vary from point to point within a body and are dependent on the internal torques at the individual points and geometric section properties. Internal torques can be found by sectioning bodies and applying equilibrium equations, just like we did axial loading problems (see examples 1.5, 2.1 and 2.2). In the case of internal torques, moment equilibrium around the longitudinal axis will be applied instead of force summation.
Before looking at an example that illustrates the process of finding internal torque reactions, it would be beneficial to establish the sign conventions that will be used as well as ways of representing torque in this text.
6.0.3 Sign Convention and Representation of Torque
Just as is typically used for moments, the sign convention that will be used in this text for torques is to assign a positive sign to torques that are counterclockwise and a negative sign for those that are clockwise. However, the direction that a torque appears to be depends on the perspective from which the rotation is being observed. In Figure 6.5 below, the applied torque would appear clockwise if viewed from the left end of the bar towards the right and counterclockwise if viewed from the right end of the bar towards the left. As long as one is being consistent, it is not usually important which perspective is used. However, a typical convention is to look from the free end of the shaft if there is one, towards the fixed end, or from the positive longitudinal axis if one is given, towards the negative.
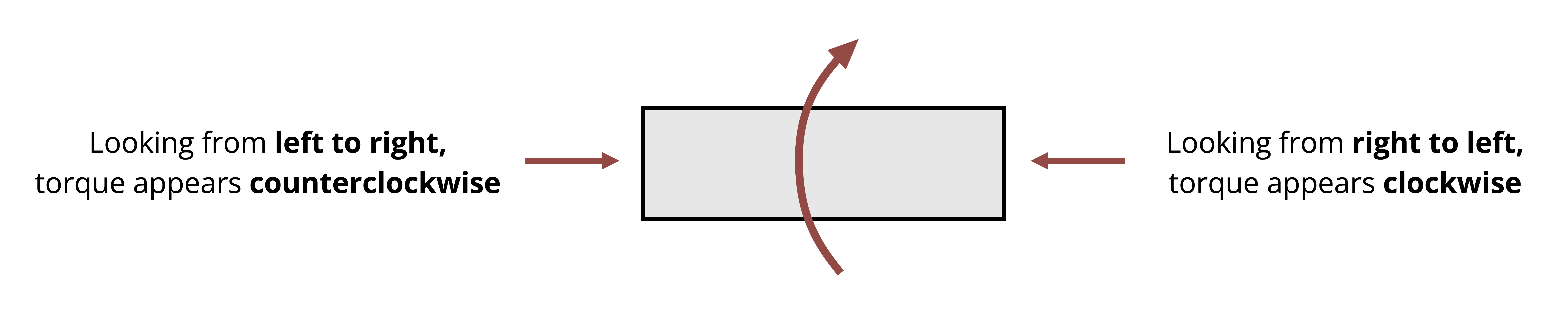
It can sometimes be difficult to visually determine whether a torque appears clockwise or counterclockwise, so one tool that can be used is the right-hand rule. If you use your right hand and curl your fingers in the direction of the rotation represented by the torque arrow, a positive (counterclockwise) torque would be represented if your thumb points in the direction of the positive longitudinal axis (the x-axis in Figure 6.6).
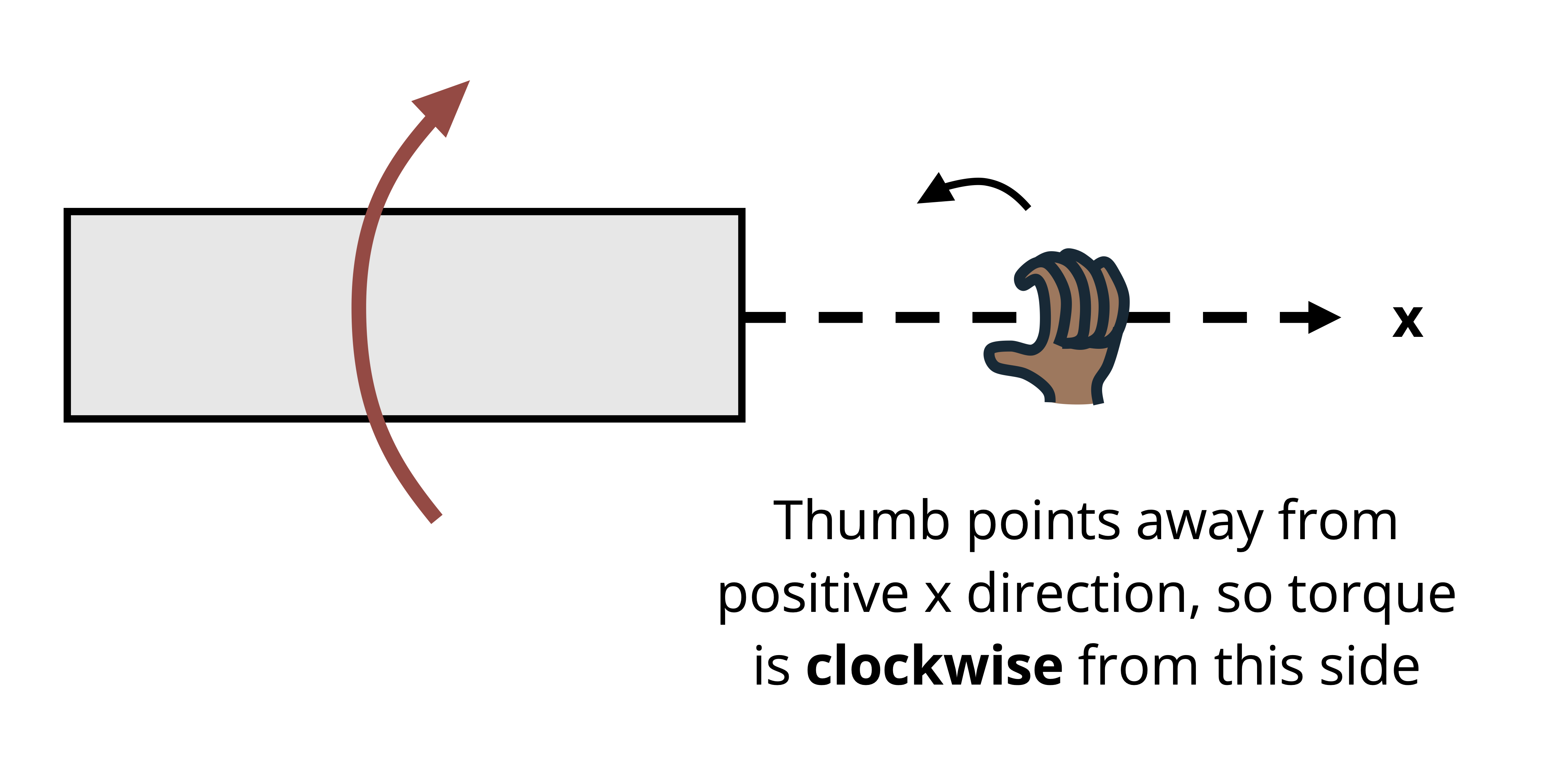
When examining cut sections as will be needed to determine internal torques, establishing the sign of the internal torque requires looking from the direction of the cut edge towards the end of the cut section. One tool that can be used in this instance in place of direction visualization is to make the cut necessary to determine the internal torque in a given section and then imagine your right hand as being at the cut edge and curl your fingers in the direction of the torque. If your thumb points away from the cut edge, the internal torque is positive and vice versa. This is illustrated in Figure 6.7.
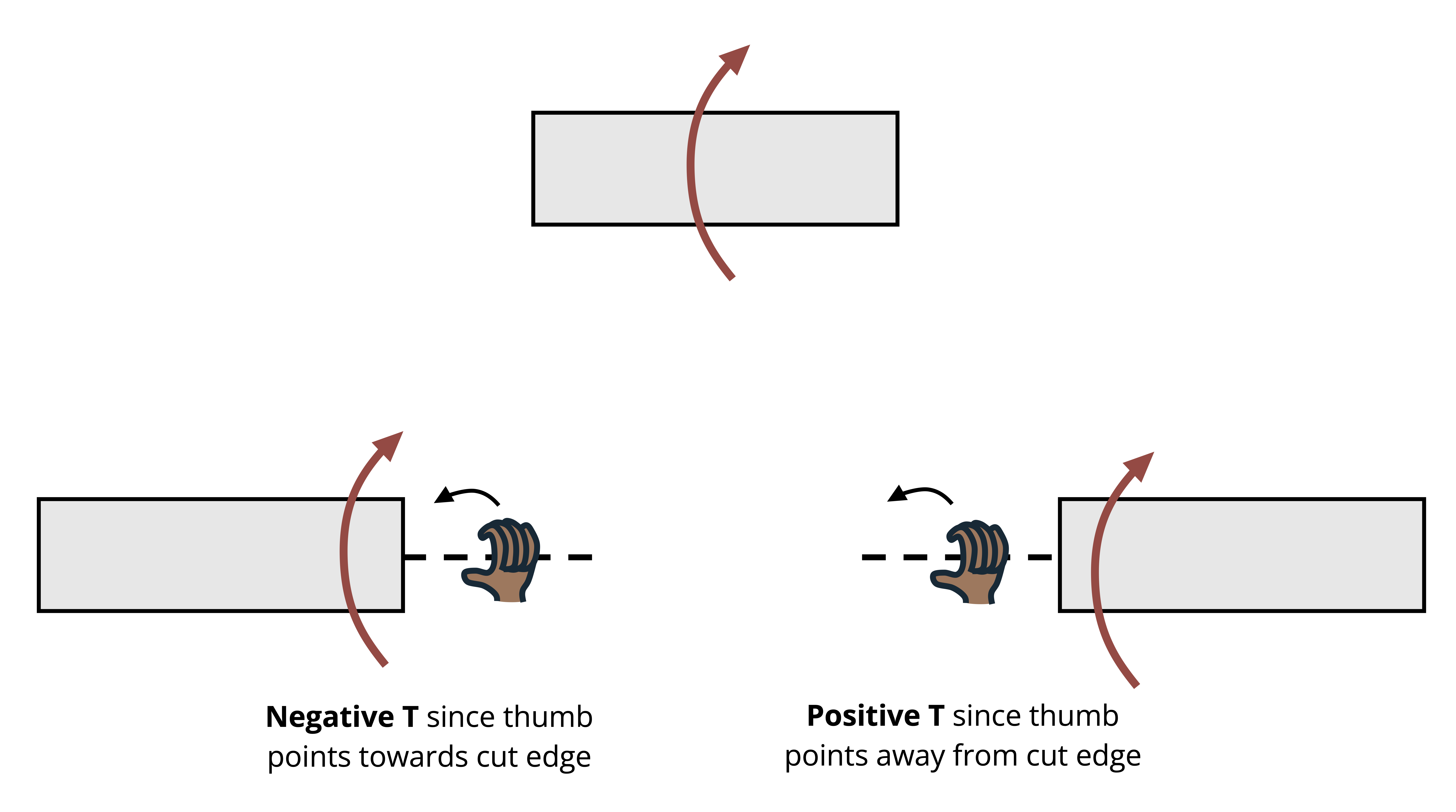
Finally, since circular arrows can be difficult to draw in a way that clearly conveys direction, double headed line arrows are frequently used to represent torque. Conventions can vary between texts and other sources. In this text, the following convention will be used:
- On a whole body FBD, arrows facing in the direction of the positive longitudinal axis will be considered to indicate positive torques (counterclockwise) and vice versa. When applying equilibrium, these signs will be used.
- The same will hold true for cut section FBD’s used to determine internal torques. However, if applying equilibrium indicates that the internal torque points away from the cut section, the torque can be concluded to be positive (counterclockwise) for the purposes of calculating angle of twist. Internal torque that points towards the cut section can be concluded to be negative (clockwise). In addition, on the cut sections, the regular convention of right directed arrows being positive and left directed arrows being negative for the purpose of summing moments will be used.
The direction of the internal torque is not important in calculating shear stress (the sign on the stress requires concepts that will be discussed in Chapter 12), but it is important when calculating angle of twist, as we’ll see in Section 6.2.
Example 6.1 demonstrates how to determine internal torques in a multi-section body as well as how to apply the above-described sign conventions.
6.1 Calculation of Shear Stress due to Pure Torsion
Click to expand
In this section, the derivation of the shear stress equation for torque is explained before presenting it so that the inputs to the resulting equation, as well as the assumptions, etc., can be better understood.
Consider a circular shaft that is fixed on one end and subjected to torque on the free end, as shown in Figure 6.8. The shaft has an outer radius, c, as shown in Figure 6.9 (B). For the given loading, the internal torque at any location along the shaft, x, would also be T.
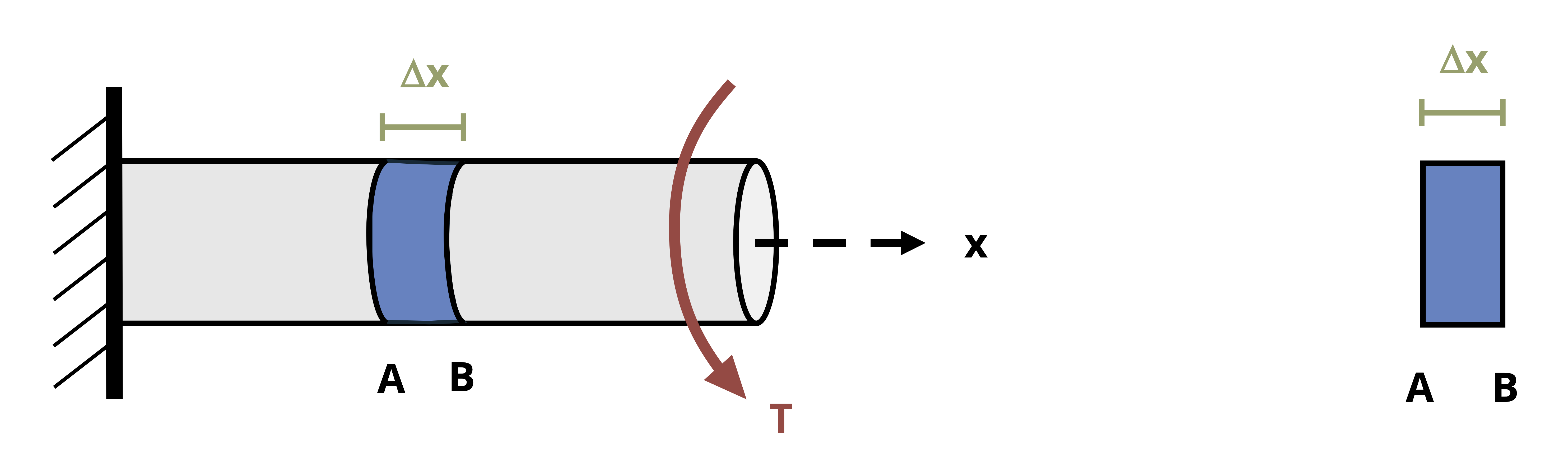
Before the torque, T, is applied, a horizontal line segment drawn across a sliver of the shaft, marked by points A and B, has a length of Δx. Now let’s consider the same shaft segment after the torque has been applied and points A and B move to A’ and B’. An illustration of the resulting geometry can be seen in Figure 6.9 (A). Since the shaft is fixed on the left end, we see that point B on the shaft will rotate more than point A. We can approximate that line segment AB remains linear for a very narrow section of shaft (infinitely small Δx).
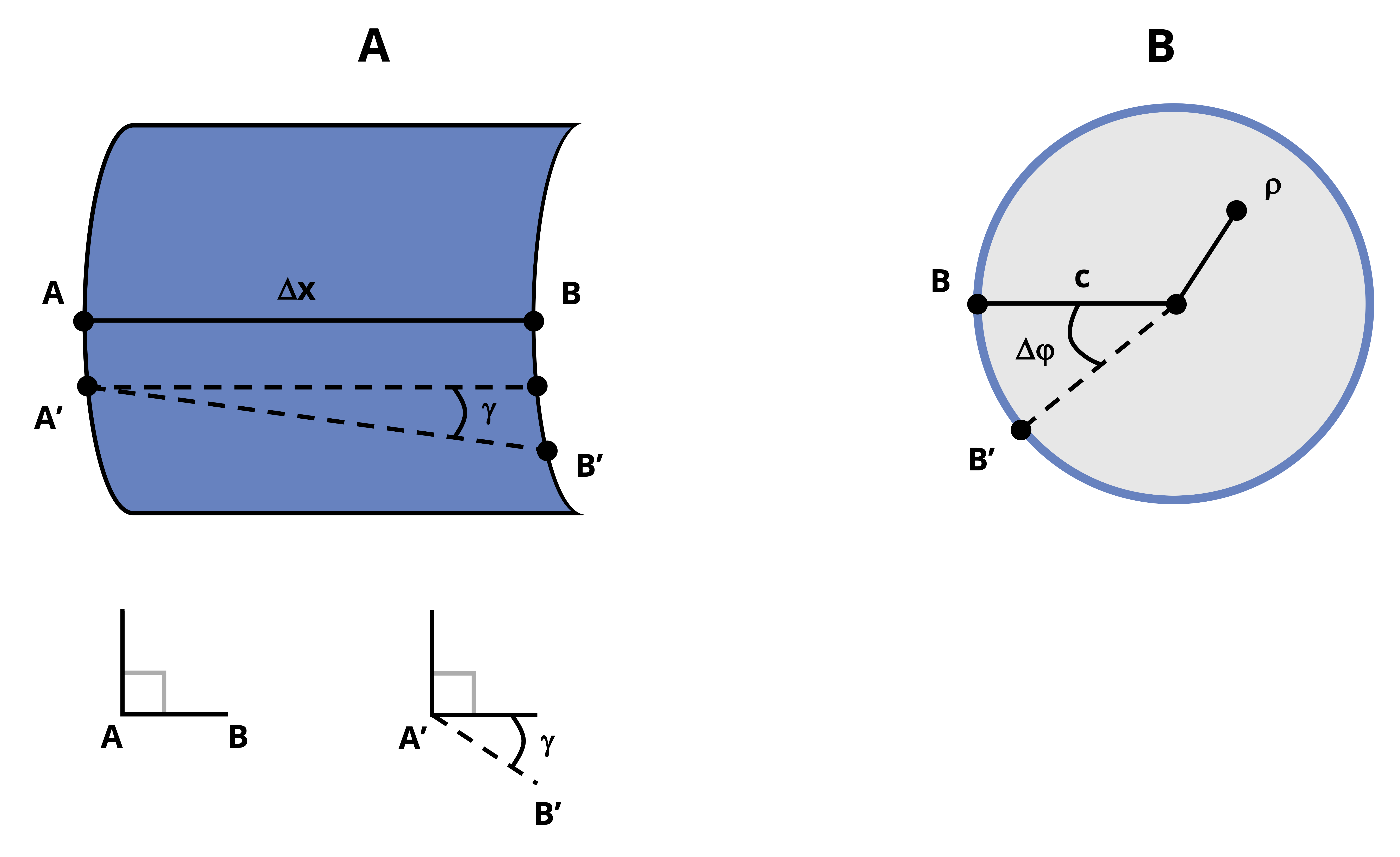
Recalling that shear strain is the change in the angle between two lines that are originally perpendicular, we can see that the angle of tilt in AB after the torque is applied is the shear strain, γ, that results from the torque. The displacement of point B from the original position to B’ on the cross-section is shown in Figure 6.9 (B). For an infinitely small Δx, the arc segment from B to B’ can be approximated as vertical so that the shear strain γ can be expressed using trigonometry as:
\[ \tan (\gamma)=\frac{B B^{\prime}}{\Delta x} \]
The small angle approximation (again, based on an infinitely small Δx), gives:
\[ \gamma=\frac{B B^{\prime}}{\Delta x} \]
Now consider the cross-section of the shaft where point B and B’ are located, shown in Figure 6.9 (B). As discussed above, B’ is the location point B moves to when the torque is applied, so the angle between the radial lines that go from the center to points B and B’, respectively, of the shaft segment is the angle of twist of the segment. Since we are considering just a section of the shaft, the angle is represented as Δφ (as opposed to the absolute angle of twist, φ, as measured from the fixed end). If the outer radius of the shaft is r = c, then the length of BB’ is given by the arclength, so:
\[ \mathrm{BB}^{\prime}=\mathrm{c}(\Delta \phi) \]
and
\[ \gamma=\frac{c(\Delta \phi)}{\Delta x} \]
Generalizing this result for any point on the cross-section that is located at an arbitrary radial distance ρ from the center gives:
\[ \gamma=\frac{\rho(\Delta \phi)}{\Delta x} \]
The resulting expression of γ shows that the shear strain varies linearly with ρ from the center of the cross-section to the outer radius, as illustrated in Figure 6.10. The shear strain is 0 at the center, and the max shear strain occurs at the max value of ρ = c.
\[ \gamma_{\max }=\frac{c(\Delta \phi)}{\Delta x} \]
Substituting the general and max expressions for shear strain into Hooke’s Law for shear stress, τ = Gγ, reveals that shear stress also varies linearly from 0 to τmax in going from the center of the cross-section to the outer radius.
\[ \tau=G \gamma=G \frac{\rho(\Delta \phi)}{\Delta x}, \tau_{\max }=G \frac{c(\Delta \phi)}{\Delta x} \]
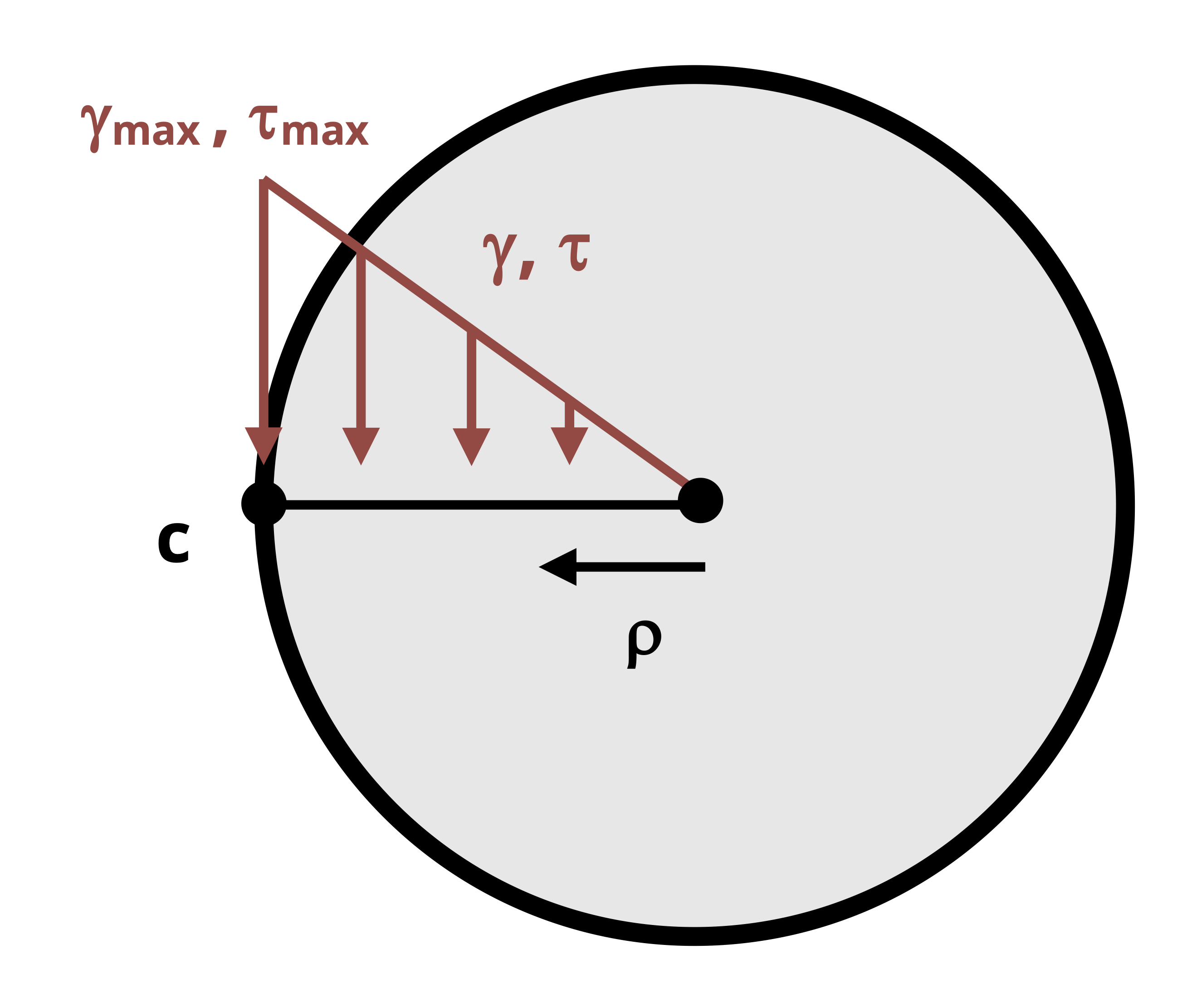
Looking at Figure 6.10 shows that the slope of the linear variation is \(\frac{\tau_{\max }}{c}\) and the shear stress can also be expressed as:
\[ \tau=\frac{\tau_{\max }}{c} \rho \]
The last step in developing the shear stress relationship to torque involves considering the equilibrium of the shaft. Refer to Figure 6.11. If each point (i) on the cross-section with area dAi has a given amount of shear stress,τi, then the corresponding force at each point dFi can be calculated as:
\[ \mathrm{dF}_i=\tau_i \mathrm{dA}_i=\frac{\tau_{\max }}{c} \rho_i d A \]
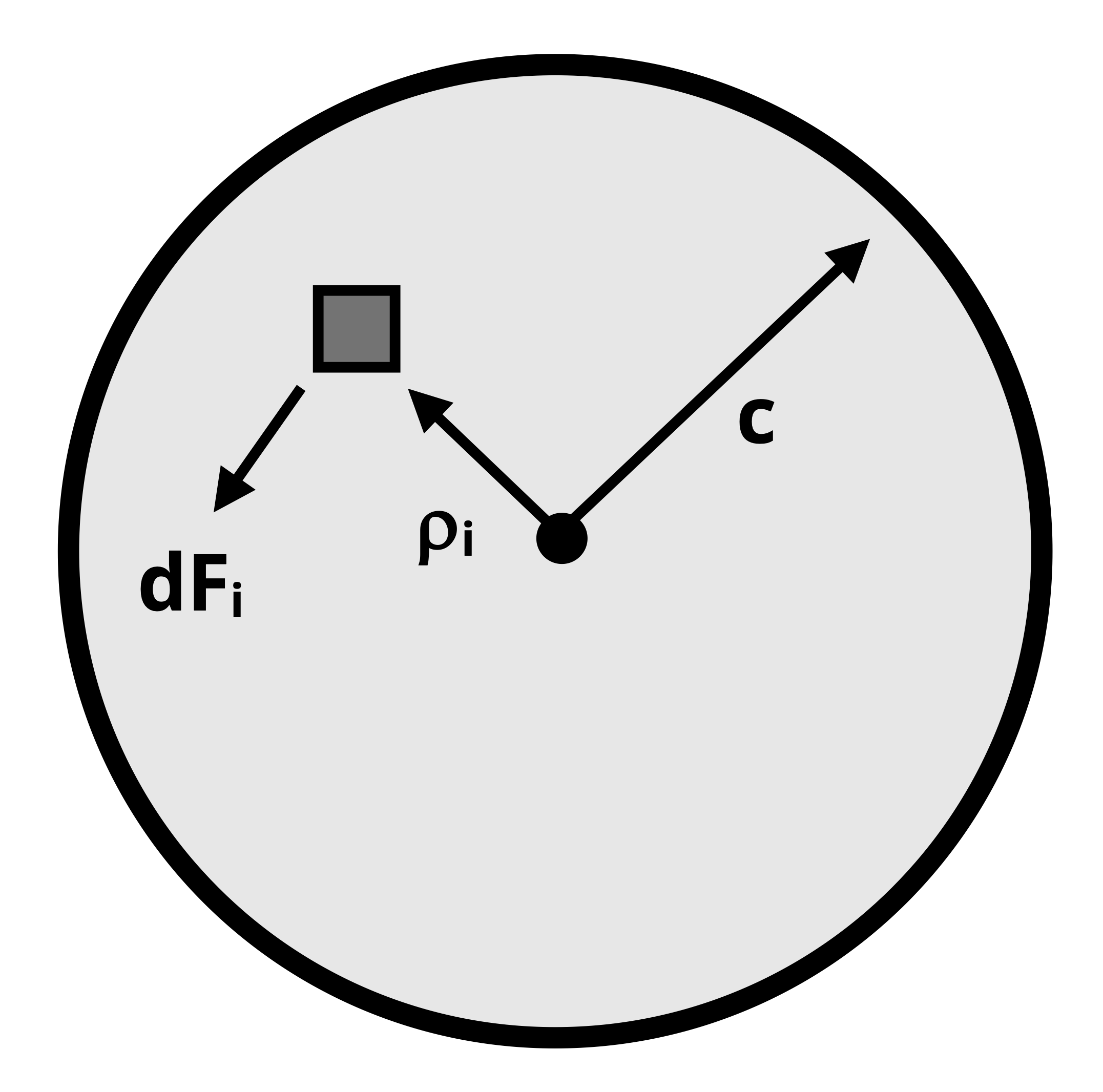
Recalling that the internal torque everywhere on the shaft is T, equilibrium dictates that the sum of the moments about the center of the cross-section should be equal to T. For an infinite number of points on the cross-section, this summation can be performed as an integral:
\[ T=\int d F_i \rho_i=\int \frac{\tau_{\max }}{c} \rho_i^2 d A \]
Since τmax and c are constant, they can be pulled outside the integral, leaving the integral portion to be \(\int \rho_i^2 d A\), which is the definition of the polar moment of inertia. The polar moment of inertia is the moment of inertia around the out of plane axis, which is the x-axis. The polar moment of inertia will be denoted with the letter J in this text.
For a solid circular cross-section of outer radius, r, and outer diameter, d:
\[ J_{solid}=\frac{\pi}{4} r^4=\frac{\pi}{64} d^4 \]
For a tube or hollow circular cross-section with outer radius and diameter, ro and do, respectively, and inner radius and diameter, ri and di, respectively:
\[ J_{hollow}=\frac{\pi}{4}\left(r_o^4-r_i^4\right)=\frac{\pi}{32}\left(d_o^4-d_i^4\right) \]
Replacing \(J=\rho^2_idA\) in our previous equation gives:
\[ T=\frac{\tau_{\max } J}{c} \]
This can be rearranged to:
\[ \tau_{\max }=\frac{T c}{J} \]
This equation gives the maximum stress on a given cross-section, which will occur on the outer edge of the shaft (where \(\rho=c\)). A more general form of the equation which can be used to find the stress at any point on the cross-section is:
\[ \boxed{\tau=\frac{T \rho}{J}} \tag{6.1}\]
𝜏 = Shear stress due to torsion [Pa, psi]
T = Internal torque [N·m, lb·in.]
𝜌 = Radial distance from center of cross-section to point of interest [m, in.]
J = Polar moment of inertia [m4, in.4]
Note that for now, only the magnitude of the shear stress (without sign) will be determined since the sign for shear stress is not based purely on the sign of the torque. The sign on shear stress will be discussed in Chapter 12.
Example 6.2 demonstrates the use of the above equations to determine shear stress in the same circular bar assembly used in Example 6.1.
6.2 Calculation of Angle of Twist
Click to expand
In Chapter 5, we derived and applied a formula for axial deformation. We will do something similar in this chapter for circular shafts subjected to torsion. The deformation of a shaft that arises from applying torsion, assuming deformation is restricted to the elastic deformation range for the material, is quantified by the angle of twist, \(\phi\). As discussed in Section 6.1, and illustrated here again in Figure 6.12, the angle of twist is the angle formed between the radial line that goes from the center of the cross section to a point in its original location and the radial line that goes from the center to the point in its new location after the torsional load is applied. The equation to determine angle of twist at various points along the shaft will be derived below.
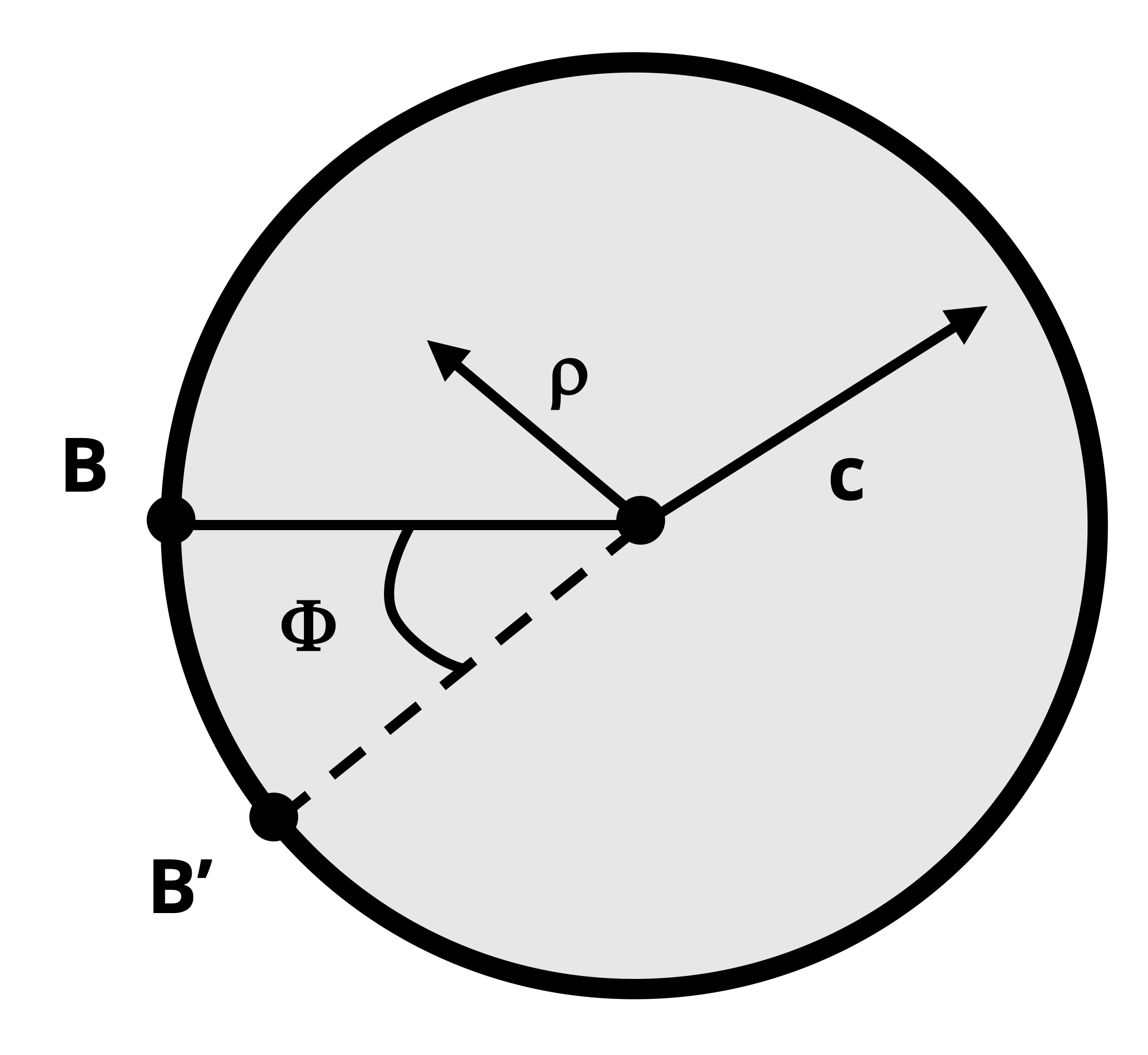
Recall from Section 6.1 that the shear strain \(\gamma=\frac{\rho(\Delta \phi)}{\Delta x}\). Also recall that Δx represents the length of a section of shaft of arbitrary length and Δφ is the change in angle of twist that occurs across that length. For an infinitely small section of shaft, the shear strain equation can be expressed in terms of differentials: \(\gamma=\frac{\rho(d \phi)}{d x}\).
Now applying Hooke’s Law, τ = Gγ, and the equation for shear stress we get:
\[ \frac{\rho(d \phi)}{d x}=\frac{\tau}{G}=\frac{T \rho}{J G} \]
Solving for dφ gives:
\[ d \phi=\frac{T d x}{J G} \]
For a section (i) of shaft of length Li for which torque (Ti), material (Gi), and geometry (Ji), stay constant, this becomes:
\[ \phi_i=\frac{T_i L_i}{J_i G_i} \]
Integrating both sides of the equation gives the total angle of twist for an entire shaft or section of shaft:
\[ \phi=\int \frac{T d x}{J G} \]
For multi-section bodies where each individual section has constant T, J, and G, the integral can be expressed in the form of a sum where the angle of twist of each distinct section is calculated individually and then they are all added together:
\[ \boxed{\phi=\phi_i=\sum \frac{T_i L_i}{J_i G_i}} \tag{6.2}\]
𝜙 = Change in angle [rad]
T = Internal torque [N·m, lb·in.]
L = Length [m, in.]
J = Polar moment of inertia [m4, in.4]
G = Shear modulus [Pa, psi]
In these calculations, the sign of internal torque will be important as it indicates the direction of the twist. If one section twists in one direction and the adjoining section twists in the opposite direction, the effect will be that the angles will subtract from each other resulting in a smaller overall angle of twist. On the other hand, if two adjoining sections twist in the same direction, the effect will be additive. According to the assigned sign convention discussed in Section 6.1, an overall positive angle of twist indicates that the shaft twists counterclockwise when looking from the positive end of the longitudinal axis to the negative and vice versa.
6.2.1 Units
If values for T, L, J, and G are used in Equation 6.2 such that the units are all consistent with each other, the overall unit works out to be unitless as is expected for an angle calculation. Since the calculation is for an angle, the actual unit is considered to be radians. If an angle is desired to be in degrees, the result of the equation would need to be converted by multiplying the result by π/180.
Because the angle of twist often works out to be very small, it may be desired to express the value in terms of μrad, which is 10-6 radians. To convert from rad to μrad, multiply the number of radians by 106.
6.2.2 Notation
When finding the angle of twist, the angle at any given point along the length of the shaft will be found relative to some reference point. Often the reference point is a fixed point (at a fixed support for example), so the relative angle is an absolute angle. In this case, the symbol \(\phi\) will be subscripted with the point along the shaft where the angle was calculated. For example, given the shaft assembly in Figure 6.13 below, the notation φB denotes the angle of twist at point B relative to the fixed point A.
If one is finding the relative angle of twist between two non-fixed points that are on the same section of shaft (same T, J, and G), the angle of one point relative to another on the same section of shaft is notated with two subscripts specifying the two points. For example, the angle of twist of D relative to C in Figure 6.13 is notated as \(\phi_{CD}\). In this case, one would perform the calculation for the angle of twist at D as if point C is fixed, in which case:
\[ \phi_{B C}=\frac{T_{C D} L_{C D}}{J_{C D} G_{C D}} \]
If one is finding the relative angle of twist between two non-fixed points (let’s say B and D in Figure 6.13) that are on different sections of shaft (i.e., there are 1 or more section changes between them due to changing T, J, or G), the relative angle of twist between them would be found by summing the angles of twist of each section between them. In this case, the notation would be \(\phi_{D/B}\) which is said as the angle of twist of D relative to B. If point C is where the section change occurs, the calculation would be:
\[ \phi_{D / B}=\phi_{B C}+\phi_{C D} \]
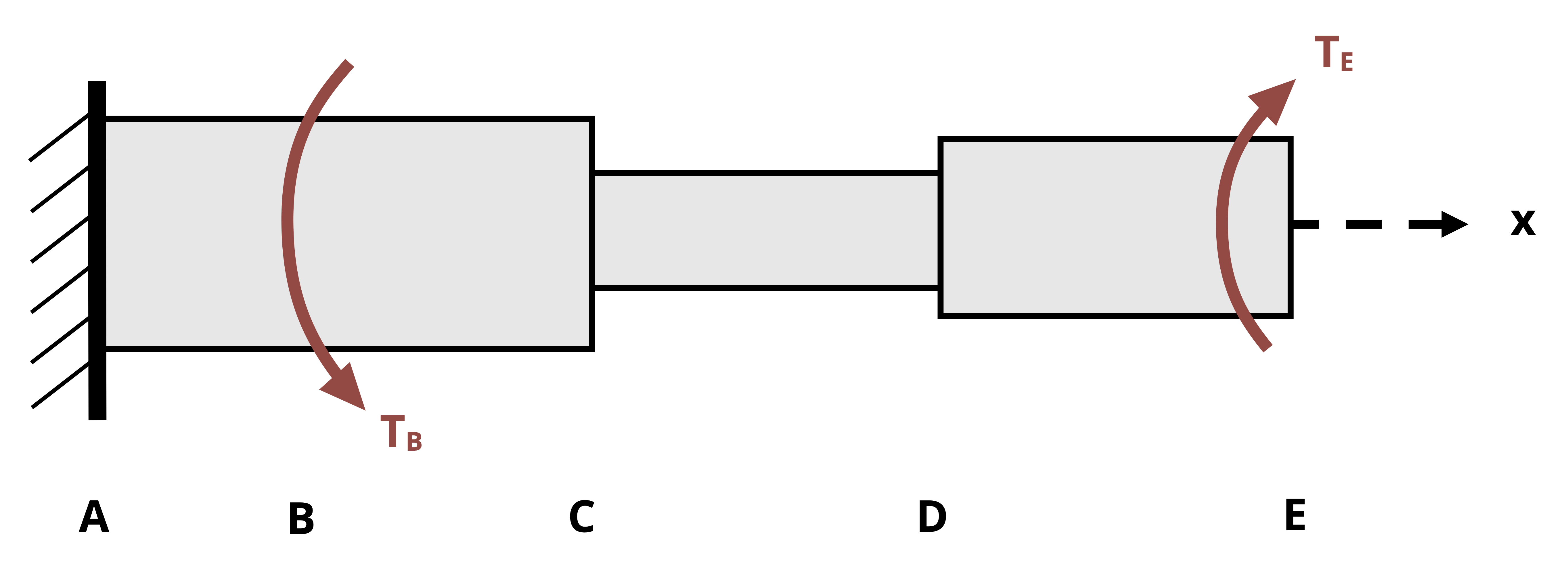
These concepts will be illustrated in Example 6.3 which continues with the same bar assembly and loading used in Example 6.1 and Example 6.2.
6.3 Statically Indeterminate Torsion
Click to expand
As was discussed in Section 5.5 for axial loading, one may sometimes encounter loading and constraint conditions that are statically indeterminate. In these situations, though a structure may be in static equilibrium, equilibrium equations do not provide enough equations to solve for all the unknown reactions. In many cases, the known constraints on deformation can be used to provide the additional necessary equations. We will consider the same two categories of statically indeterminate loading:
Redundant supports—Cases where there are fixed supports at each end. In this configuration, the shaft is constrained on both ends such that the overall angle of twist must be 0 if both ends are truly fixed, or the angle of twist is limited to a specified amount if there is a fixed degree of freedom on one end (for example if one side involves a loose connection).
Co-axial or parallel shafts—multiple shafts are bonded concentrically (one within another) so that they are constrained to twist as a unit by the same amount. In this case, the extra equation needed in addition to equilibrium comes from setting the angle of twist for each material equal to each other.
6.3.1 Method of Superposition
For the case of redundant supports, an alternative would be to use the method of superposition. The method of superposition is based on the idea that the effects of individual loads on the deformation of a body can be calculated individually and then added together to get the total effect. To apply this method:
- Take away one of the redundant supports
- Determine the total angle of twist of the shaft without the support
- Replace the support but take way the other loads
- Determine the deformation in the shaft due to the reaction at the now replaced support
- Sum the angle of twist from step 2 and step 4 and set the total equal to zero (or a given angle as appropriate).
- Solve the equation resulting from step 5 for the reaction at the redundant support and then use the whole body equilibrium to solve for the reaction at the other support(s).
Example 6.4 demonstrates how to solve a statically indeterminate torsion problem that falls under the first category of problems described above. Example 6.5 uses superposition to solve part (a) of Example 6.4.
Example 6.6 goes through the process of solving a statically indeterminate torsion problems that falls under the second category of problems described above.
6.4 Power Transmission
Click to expand
As mentioned in the introduction to torsion, one common application in which one would encounter circular shafts subjected to torsion is in power transmission shafts. In these types of assemblies, shafts are connected through gears and belts and apply torque to one another through these connections. If a shaft somewhere in the assembly is connected to a motor that causes it to rotate, that rotation is then transmitted to other connected shafts which can in turn transmit rotation to even more shafts. Note that such systems are still considered to be in equilibrium even with the rotation as long as the angular velocity is constant.
6.4.1 Definition of Power
You may recall from other subjects of study that power is defined to be the time rate of change of work. The definition of work is force times distance. So power can be calculated as:
\[ P=\frac{W}{t}=\frac{F \times d}{t} \]
Within the context of rotating shafts, the force would be the force applied to the outer edge of the shaft that results in torque and the distance would be the arc length that a point on the edge of the shaft travels around the circumference in a given amount of time, t. Figure 6.14 illustrates this point.
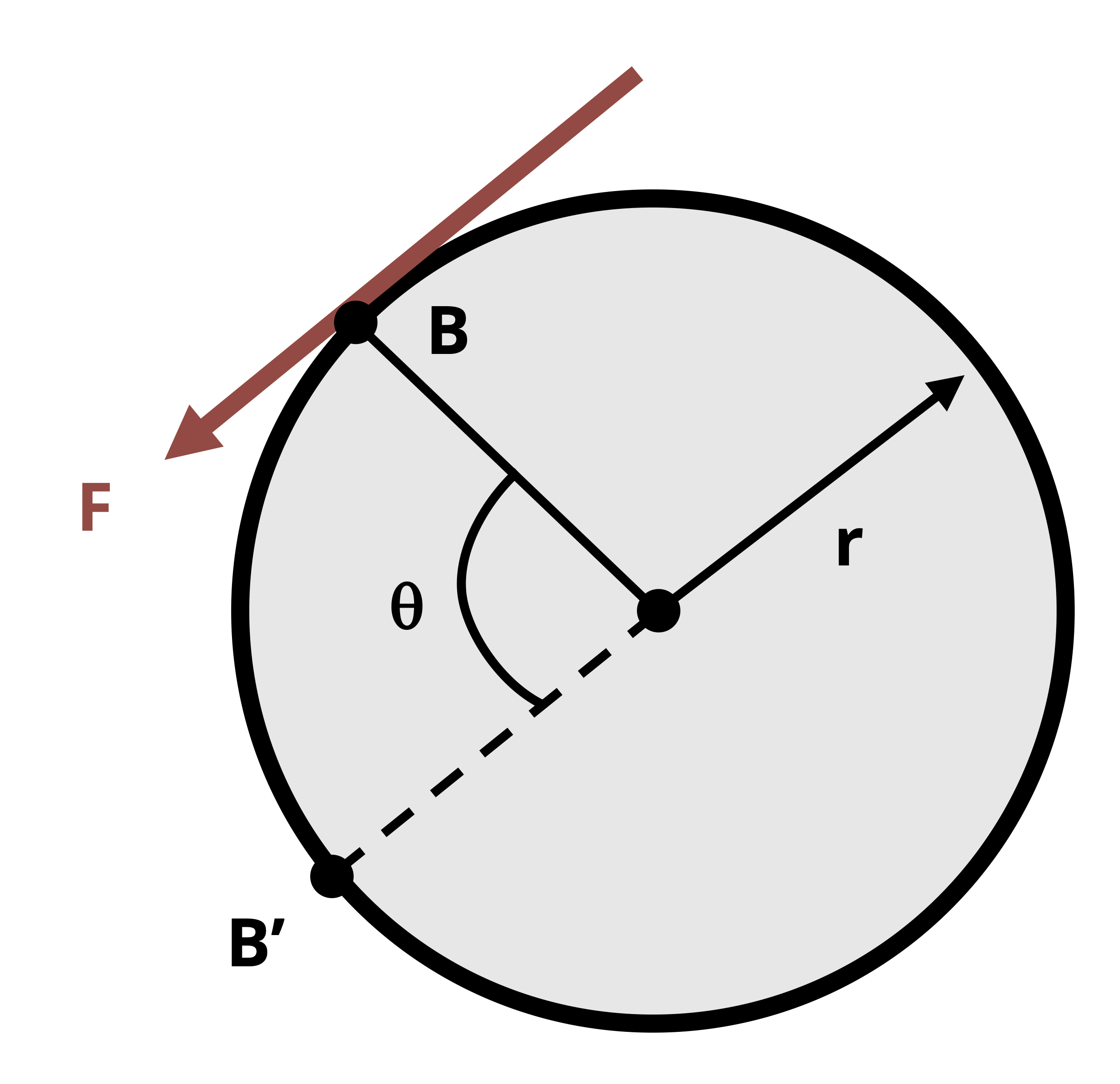
If the arclength over which point B travels, BB’ = rθ, then W = Frθ. However, Fr is also equal to the torque T on the shaft, so W = Tθ.
Going back to the power equation, we then have \(P=\frac{T \theta}{t}\). The \(\frac{\theta}{t}\) is angular velocity, which will be denoted with the Greek letter ω. So the power equation can finally be expressed as:
\[ \boxed{P = T\omega} \tag{6.3}\]
P = Power [Watts, horsepower]
T = Torque [N·m, lb·in.]
𝜔 = Angular velocity [rad/sec]
6.4.2 Units
In SI the standard unit for power is the Watt (W), which is (N·m)/s. The N·m unit is also referred to as a Joule, so a Watt is a Joule/s.
In US Customary units, power is commonly expressed as ft·lb/s or in·lb/s. However, it is also common to express power in terms of horsepower, where there are 550 ft·lb/s for 1 hp. Note that there is a conversion difference between the US horsepower and the British horsepower. In this text, horsepower will refer to the US version.
When applying the P = Tω equation, the angular velocity ω must be expressed in radians per second. If frequency is given in Hz, which is 1 revolution/s, then one must multiply by 2π to convert it to rad/s since there are 2π rad per revolution.
If angular velocity is given in rpm, which is revolution per minute, then one must multiply by 2π radians per revolution and divide by 60 to convert 1/min to 1/s. This reduces to an overall multiplication factor of π/30 to convert from rpm to rad/s.
SI (watt) | \[ W=\frac{N m}{s}=\frac{J}{s} \] |
US | \[ \left(\frac{f t l b}{s}\right) \operatorname{or}\left(\frac{l b}{s}\right) \] |
US (horsepower, hP) | \[ 1 h P=\frac{550 f t l b}{s} \] |
Hertz (Hz) | \[ H z=\frac{r e v}{s} \] |
Angular velocity given Hz (rad/s) | \[ \frac{r a d}{s}=H z(2 \pi)=\frac{r e v}{s}(2 \pi) \] |
Angular velocity given rpm (rad/s) | \[ \frac{\mathrm{rad}}{\mathrm{s}}=\frac{r e v}{\min }\left(\frac{2 \pi \mathrm{rad}}{1 \mathrm{rev}}\right)\left(\frac{1 \mathrm{~min}}{60 \mathrm{~s}}\right) \] |
6.4.3 Torque Transfer Between Connected Gears (Gear Ratio)
Consider two connected gears as shown in Figure 6.15. The interaction of the teeth results in a force applied to each gear from the other. For equilibrium, this force must be equal in magnitude but opposite in direction. The force results in a torque which can be expressed as T = Fr.
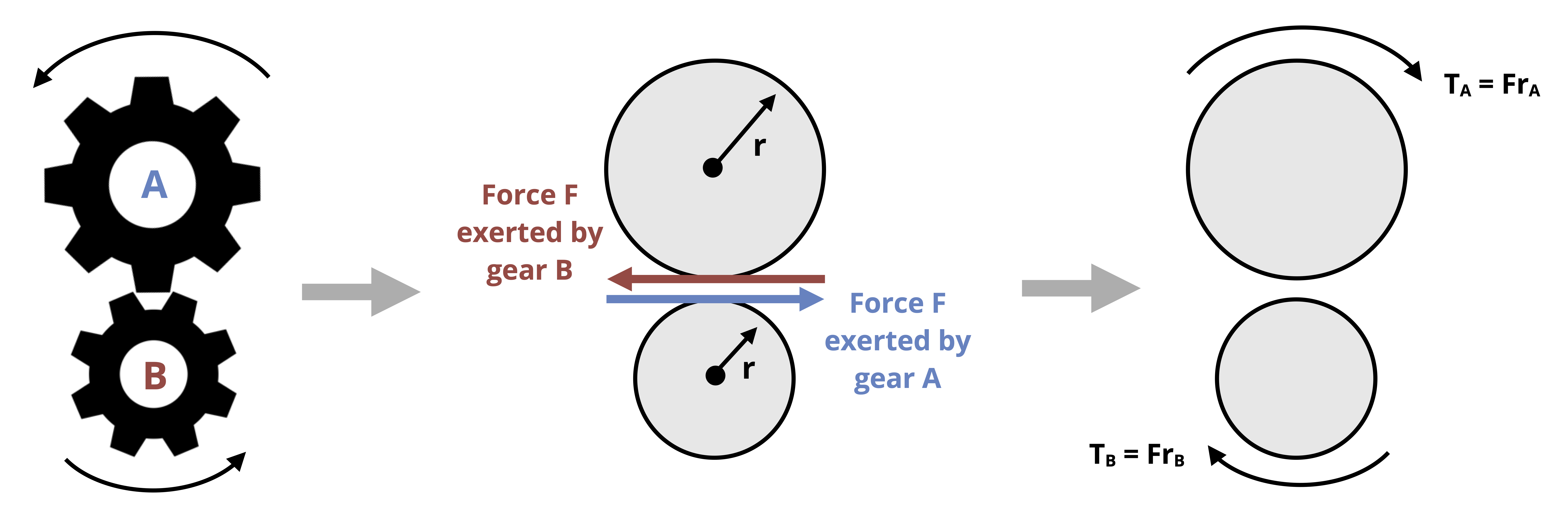
Given that the force on each gear is equal in magnitude to the force on the other, we can write:
\[ F=\frac{T_A}{r_A}=\frac{T_B}{r_B} \]
which then allows us to express the torque exerted by one gear in terms of the torque exerted by the other as well as the ratio of radii:
\[ \boxed{T_A=\frac{r_A}{r_B} T_B} \tag{6.4}\]
The ratio of radii is known as the gear ratio. It can be expressed in terms of the ratio of gear radii, gear diameters, or the number of teeth on each gear.
6.4.4 Angular Velocity Ratio of Connected Shafts
When two shafts are connected by a pair of gears, conservation of energy would dictate that the power transferred into one shaft equals the power transferring out of the other (power in = power out, assuming losses are negligible).
So if PA = TAωA and PB = TBωB and PA = PB, then we get \(\omega_A=\frac{T_B}{T_A} \omega_B\)
Further using the gear ratio relationship between TB and TA gives:
\[ \boxed{\omega_A=\frac{r_B}{r_A} \omega_B} \tag{6.5}\]
Note that the gear ratio in this case is inverse of the one used to relate torques.
6.4.5 Angle of Twist
When two connected gears rotate, they will have equal arclengths of travel for a given amount of shaft rotation, but in opposite directions, as depicted in Figure 6.16. This means that rAφA = - rBφB, and the angle of twist at point B for the shaft that it is on can be related to the angle of twist at the same location on the shaft that gear A is on.
\[ \boxed{\phi_A=-\frac{r_B}{r_A} \phi_B} \tag{6.6}\]
As with the angular velocities, notice that the gear ratio is the inverse as that used to relate torques.
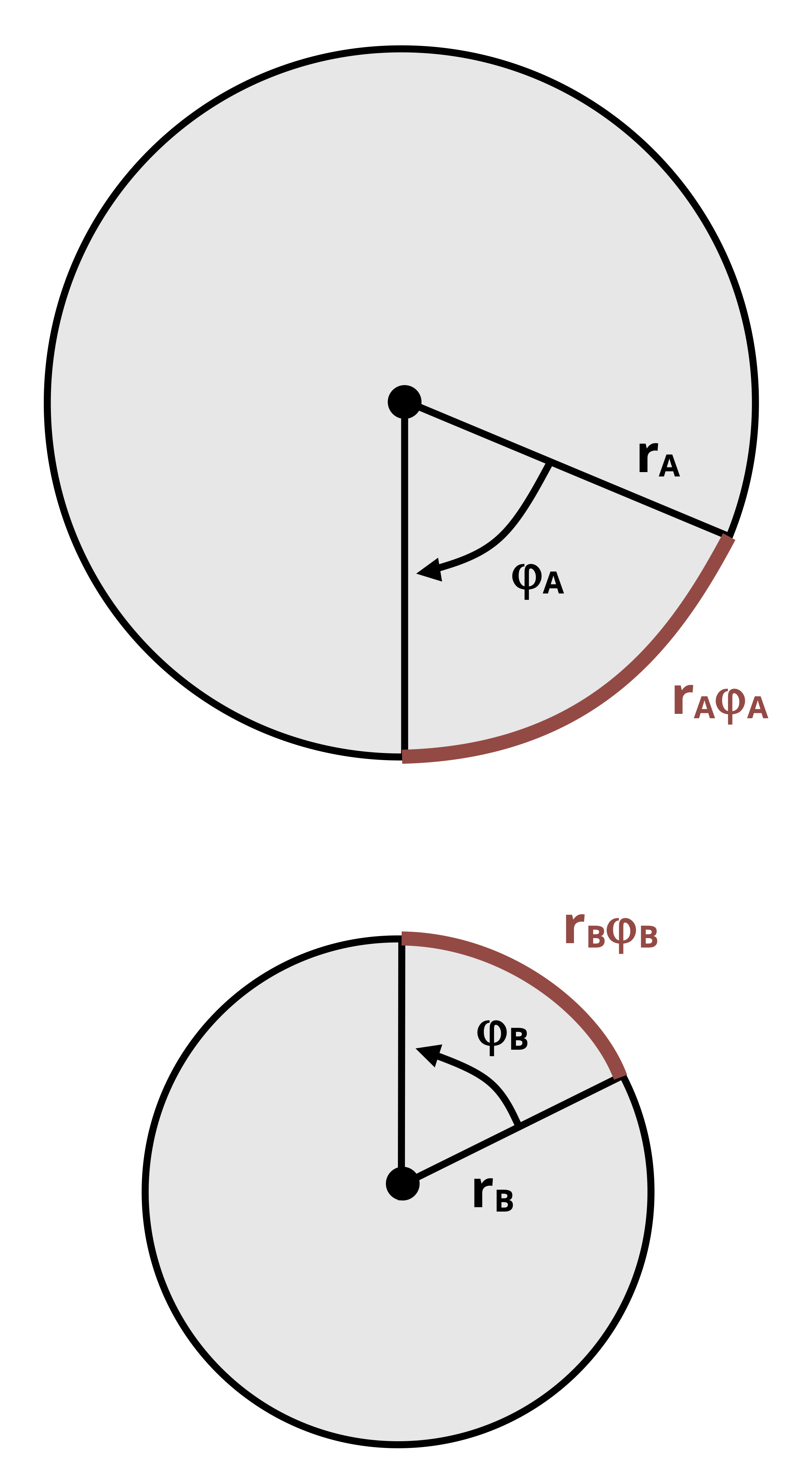
In Example 6.7, a problem of power transmission with connected gears is presented which utilizes the above concepts.